組成有Ai、Si、Mg和Ca等,同時還含有F、CI。主要物相為氮化鋁、氧化鋁、金屬鋁、鎂鋁尖晶石、方鎂石、石
英、碳化鋁及鹽溶劑等。其中氮化鋁含量10~40%、氧化鋁15~30%、單質鋁2~15%。
之間,同時還含有氟化鹽,氯化物等有毒有害物質。所含氮化鋁與水接觸或受潮濕環境的影響容易發生水解反
應,釋放出氨氣和氮氣等,對大氣造成污染并形成安全隱患。
15%~75%之間,利用價值較高,受到企業重視并得到回收利用。目前對鋁灰的資源化利用主要是對一次鋁灰的
利用,被用于提取金屬鋁、生產氧化鋁、硫酸鋁、PAC/PAFC、PAS/PAFS、六氟鋁酸鈉等。其它還被用于生產棕
剛玉、石油壓裂支撐劑、陶瓷、耐材等。
理。這不僅造成了鋁資源的極大浪費,而且對環境與安全也形成了危害。
二次鋁灰無害化處置與資源化利用技術,既是環境保護的需要,更是企業可持續發展的需要。
含有氮化鋁與水反應生成的氨氣所形成的堿性溶液,所述堿性溶液的pH值在8~10之間。根據有關標準,pH≥12.
5,≤2.0時固體廢棄物具有腐蝕性。由此可知二次鋁灰不具有腐蝕性。
生成氫氧化鋁和氨。實驗可知,二次鋁灰與水反應釋放的氨氣量較大。氨氣是一種有刺激性的氣體,空氣中濃
度較高時會對人體造成損害,甚至導致死亡。氨氣的釋放對生態環境和生命健康有一定危害。二次鋁灰中所含
毒性物質主要為氟化物、氯化物等。毒性浸出實驗證明,二次鋁灰中氟化物、氯化物毒性浸出濃度較高,超過
標準限值,具有浸出毒性。
入《國家危險廢棄物名錄》。對二次鋁灰進行無害化處置勢在必行。
化鋁和氨氣,氨氣溶于水或逸出,過濾后得脫氮濾餅。該工藝雖然可以使鋁灰中的氮化鋁得到一定程度的分解,
使處理后的鋁灰中氮化鋁含量明顯降低。但如果不能對所產生的氨氣進行有效控制和回收,那么將會對大氣環
境造成二次污染。同時,反應生成的氫氧化鋁膠體會對氮化鋁微粒形成包裹,影響水與氮化鋁之間水解反應的
順利進行,使除氮效果受到限制。
水解反應。高溫加快了反應速率,也提高了水解效率,對水解過程所產生的氨氣進行吸收,可以收得氨水或銨
鹽。但存在的問題是水解反應需在高溫條件下進行,能耗較高。而且缺少對水解液中氟、氯元素進行分離提取
的可靠方法,所產生的廢水會對環境造成二次污染。
氧化鋁與氨的同時將氨轉化為銨鹽,經過濾得脫氮鋁灰和含有銨鹽的溶液。但由于該工藝缺少對含銨溶液及氟、
氯有害物質的處置方法,仍然存在環境隱患。
無害,先進、實用,適用于鋁冶煉及加工企業的二次鋁灰無害化處置與資源化利用技術既是環境保護的需要,
更是企業可持續發展的需要。
件下使鋁灰中的氮化鋁、鋁與水發生水解反應,所產生的氨和氫氣逸出,其中氨經吸收制得氨水。反應過程通
過采用技術與裝備措施嚴格控制尾氣中氫濃度,避免進入爆炸限,尾氣達標排放。水洗過濾所得洗液含有氟化
鉀、氟化鈉、送鹽回收工序用于回收鉀、鈉、氟化合物。濾餅送預浸工序與堿浸工序所產出的浸出液,即高苛
性比鋁酸鈉溶液反應,使鋁灰中未充分水解的氮化鋁和鋁進一步水解并揮發出氨,氨逸出后經吸收制得氨水,
尾氣達標排放。預浸濾餅送后續工序用于堿浸,預浸濾液,即低苛性比鋁酸鈉溶液送鋁化合物制備工序用作生
產原料。
氟、氯脫除率分別為98.7%和98.2%,收得率分別為96.7%和97.6%。氮化鋁水解率大于99.6%,氨收得率大于99.5%。
所得產物為氯化鈉、氯化鉀、氟化鈣和氨水。
去除并收得了相關化合物,無廢水排放。通過堿溶使鋁灰中的鋁轉化為鋁酸鈉,作為生產高附加值鋁化合物的
基礎原料,具有有害物質脫除率高,處理過程安全環保,所得鋁產物利用價值高等特點。
劑(PAC/PAFC,PAS/PAFS)等。存在的問題,要么是產品附加值較低,生產企業難以獲得經濟效益。如生產PAC,
如果沒有免費的鹽酸或廢鹽酸及蒸汽來源,生產企業幾乎沒有盈利的可能。要么存在著生產過程因三廢的產生
和排放給環境造成的二次污染問題。
的循環利用為目的,以安全、環保、生產成本較低、產品附加值較高、能夠未生產企業創造經濟效益為宗旨,
河南睿博環境工程技術有限公司研發出了二次鋁灰資源化利用新工藝。該工藝以二次鋁灰無害化處置過程所制
得的鋁酸鈉為鋁源,以磷化工企業副產的氟硅酸為氟源,采用固相混合反應工藝與新型集約式同步異位氟化反
應器完成干法氟化鋁的制備。氟化反應過程產生的氨氣濃度被嚴格控制在安全范圍,并在負壓條件下被及時引
入氟硅酸氨化反應系統作為氨化劑使用,生產過程安全、環保,產品質量優于AF-1指標。
程所產出的鋁酸鈉經進一步脫硅、除鐵,再經種分、碳分制得氫氧化鋁。生產過程所得氫氧化鋁母液經苛化、
過濾、濃調收得氫氧化鈉,返回無害化處置工序用作堿溶劑。同時以廉價的氟硅酸為氟源,以氟化鋁制備工序
所產生的含氨尾氣為氨化劑,經氨化、分離制得副產沉淀白炭黑和氟化銨溶液。將氟化銨溶液濃縮、結晶、干
燥制得氟化銨。
裝制得干法氟化鋁產品。氟化反應在負壓條件下進行,所產生的氨濃為45~60%的反應尾氣經冷卻、除塵后被引
入氟硅酸氨化反應系統作為氨化劑使用。
進入爆炸限,遇到引爆火種,如靜電、明火等,則會引起爆炸。這正是氟化銨法生產干法氟化鋁所存在的安全
隱患。為解決這個問題,新工藝一是改變了氟化銨法生產干法氟化鋁的工藝運行模式,即由氟化銨熱解制備氟
化氫與氨的混合氣體,再以混合氣體中的氟化氫與氫氧化鋁進行氟化反應生產氟化鋁,改進為由氟化銨晶體與
氫氧化鋁直接混合、反應制得氟化鋁。二是配套研發出了一種新型氟化反應器,這種反應器有別于公知的流化
床反應器,運行過程將氫氧化鋁、氟化銨從設備的不同位置同步加入到反應器中,二者在反應器中分別發生脫
水和分解反應,形成固、氣之間的混合并完成氟化反應,整個反應在同一設備中完成。反應過程所產生尾氣的
成份主要為氨,被及時引出氟化反應器,經冷卻、除塵后進入氟硅酸氨化工序用作氨化劑。為防止氣體混合事
故的發生,在氟化反應器的進料口、出料口、冷卻器和除塵器進出口配置有氮封裝置,在設備不同的連接及運
轉部位安裝有其它密封裝置。使反應過程在全封閉、負壓條件下進行,由此確保了生產過程的安全性。此外,
為了避免生產運行出現意外時發生氨氣泄露事件,在氟化反應器與氟硅酸氨化反應器的管路中還安裝有反應尾
氣緊急吸收系統,以確保氨化反應運行失常時反應尾氣不外泄。通過上述措施確保了生產的安全性。
此,通過采用密閉式反應設備和封閉式雙級混合吸收方式進行吸收,收得氨水送氟硅酸氨化工序用作氨化劑。
所產生的廢水為鋁灰洗滌過程所產生的濃鹽洗出液和氫氧化鋁制備工序產生母液。洗出液主要成份為氟化物和
氯化物,送后續處理工序用于回收氯化鉀、氯化鈉和氟化鈣。氫氧化鋁母液為碳酸鈉溶液,送氫氧化鈉再生回
收工序經苛化、過濾、濃縮收得氫氧化鈉,所得氫氧化鈉返回生產系統循環用作堿溶劑。廢渣為產生于堿溶工
序和脫硅工序的硅鈣渣,數量較少、無害,收集以備綜合利用。整個生產過程通過采取相應的技術與裝備措施,
對三廢進行了有效控制和循環利用,實現了二次鋁灰無害化處置和資源化利用的綠色化。
率大于95%,收得率大于97%(以浸出率為基數),氟收得率95%,氟硅酸中硅收得率98%。生產過程氨及氫氧化
鈉循環利用率分別為95%和96.5%。
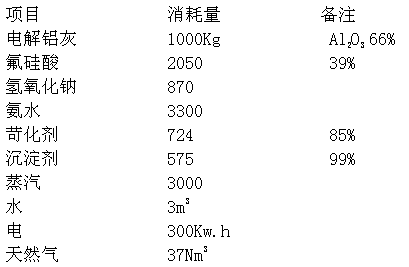
產沉淀法白炭黑359Kg,碳酸鈣1050Kg。經檢測,所得氟化鋁產品質量優于GB/T4292-2017標準中AF-1指標,其
中松裝密度在1.36~1.44g/cm3之間。
硅酸生產干法氟化鋁,大幅度提升了鋁灰的利用價值,能夠創造可觀的經濟效益,具有良好的社會效益和環境效
益。新工藝的成功研發為二次鋁灰的無害化、高值化利用開辟了一條新途徑。由鋁生產過程所產生的鋁灰生產
氟化鋁,實現了鋁冶煉及加工企業所需氟化鋁的循環自給,有利于降低生產成本,有益于鋁行業的綠色化發展。